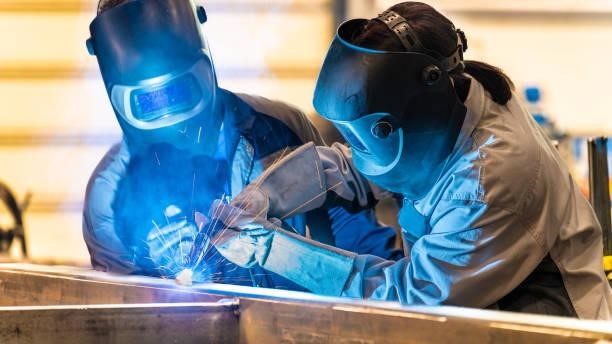
two metal fabricators welding a metal material
One of the main ways to meet or adhere to deadlines and stay competitive in sheet metal fabrication is to enhance productivity. Among the popular welding techniques, MIG and TIG welding each offer unique advantages that can affect how quickly and efficiently a project is completed. Supposedly, the right choice can streamline your workflow, saving time and money. This article explores how welding MIG and TIG compare in terms of productivity. You can choose the best technique for your welding needs by understanding all these crucial aspects.
Factors That Make a Difference in MIG Welding Productivity
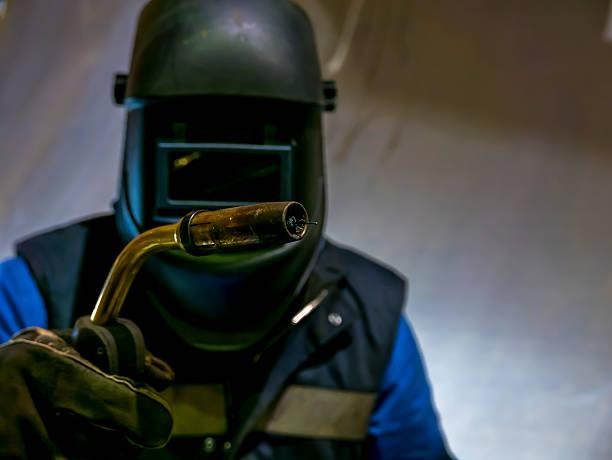
an operator holding a MIG welder torch
an operator holding a MIG welder torch
Understanding what influences MIG welding productivity helps metal fabricators streamline their processes and get better results. Several vital aspects can significantly impact how efficiently you can carry out MIG welding. Check them below:
Equipment Setup
Getting your equipment set up correctly is the first step to making sure your MIG welding operation goes smoothly. Ensuring your welding machine has the correct settings—like wire feed speed, voltage, and gas flow rates—can save time and hassle later.
Keeping your equipment in good shape also remains essential. A well-maintained machine lasts longer and works better, providing consistent performance. Investing more time in regular checks and maintenance routines pays off in the long run. Besides, simple tasks like cleaning the nozzle and replacing worn parts can prevent unexpected breakdowns, ensuring that your welding projects stay on track.
Material Preparation
How you prepare your materials can make a big difference in your welding efficiency. Clean, well-prepped surfaces help in achieving hitch-free welding with fewer defects. This not only improves the quality of the weld but also reduces the likelihood of having to redo any work. So, take the time to remove rust, oil, and other contaminants from the metal surfaces before welding.
When the surfaces are clean and free from contaminants, the weld pool can form more uniformly, leading to a better bond between the materials. Also, ensuring your materials are appropriately aligned and clamped can prevent gaps and misalignments, leading to quicker and more reliable welds.
Welder Skill Level
The skill level of the welder is another crucial factor influencing MIG welding productivity. Experienced welders can work faster and produce higher-quality welds with fewer mistakes. Investing in training programs can pay off in the long run by building a more competent and confident workforce.
Moreover, skilled sheet metal welders are better at tweaking settings and handling various welding scenarios on the fly, ensuring optimal performance even when conditions change. This, in turn, enhances productivity and provides high-quality outcomes.
Welding Technique
Techniques like maintaining the correct travel speed, angle, and distance from the workpiece can significantly impact the quality of your welds. For instance, whether you push or pull the weld can affect penetration and bead shape. Keeping your movements steady and consistent helps create uniform welds and reduces the need for cleanup after welding.
More so, fine-tuning your technique can also help reduce the occurrence of common welding defects such as porosity, cracking, and lack of fusion. By focusing on technique, welders can achieve cleaner, stronger welds with less effort and time, ultimately enhancing productivity.
Proper Use of Consumables
The consumables you use, like welding wire and shielding gas, significantly affect your productivity. Regularly checking and replacing consumables before they cause issues can help maintain smooth and efficient welding operations. Further, quality consumables reduce problems like wire feed interruptions and poor arc stability.
Hence, choose the suitable welding wire and shielding gas type for your specific application. Understanding the properties and best uses of different consumables can help you make informed decisions that boost efficiency.
Workflow Optimization
Organizing your workspace so everything you need is within easy reach can save you time and energy. You can create a well-organized and ergonomic workspace to help minimize unnecessary movements and reduce fatigue, allowing welders to work more efficiently. Additionally, implementing standardized procedures and best practices ensures consistency and reduces the likelihood of errors, further boosting productivity.
Environmental Conditions
Environmental factors like temperature, humidity, and ventilation can impact MIG welding productivity. Welding in a controlled environment helps maintain consistent conditions, reducing the likelihood of defects and rework. Good ventilation is also essential to ensure the welder’s safety and preserve the quality of the weld.
Factors That Make a Difference in TIG Welding Productivity
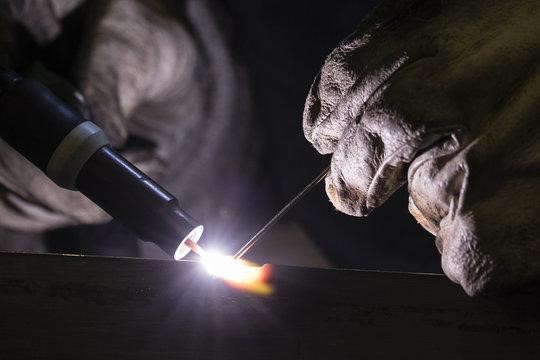
a metal fabricator welding an aluminum component with TIG welder
a metal fabricator welding an aluminum component with TIG welder
Like with MIG welding, several factors can influence the productivity of TIG welding. By paying attention to these aspects, metal fabricators can optimize their TIG welding processes and achieve high-quality results more efficiently
Here are the factors that help make a difference in TIG welding productivity:
Equipment Setup
TIG welding machines often have various settings that operators must fine-tune for optimal performance, including amperage, pulse settings, and gas flow rates. Therefore, you must ensure your equipment is correctly configured for the specific materials and thicknesses you’re working with to save time and reduce errors.
Regular maintenance of your TIG welding machine is also essential. Checking connections and keeping the torch, electrodes, and other components in good condition helps keep your equipment running smoothly.
Appropriate Use of Consumables
The consumables used in TIG welding, such as tungsten electrodes and shielding gas, are crucial. Using high-quality consumables ensures stable arc performance and reduces the likelihood of issues during welding. Regularly inspecting and replacing consumables before they become problematic helps maintain a smooth welding process.
Choosing the correct type of tungsten electrode for your specific application can also improve productivity. Different types of tungsten are better suited for various materials and thicknesses, so understanding their properties and best uses can help you make informed decisions that boost efficiency.
Material Preparation
Similarly, material preparation is critical to achieving high-quality TIG welds. Clean surfaces are essential, as TIG welding is highly sensitive to contaminants like oil, dirt, and rust. Taking the time to clean and prepare your materials thoroughly ensures better weld quality and reduces the likelihood of defects. Precise material preparation allows for smoother welding and minimizes the need for rework.
Skill Level of Welder
TIG welding requires a high level of skill and precision. Experienced TIG welders produce high-quality welds more efficiently, reducing the need for rework and ensuring consistent results. Besides, maintaining a steady hand, consistent travel speed, and the correct angle are essential for achieving quality welds.
Techniques such as proper torch control, filler rod addition, and managing heat input can impact the productivity of your TIG welds. As such, practicing and refining your welding technique helps reduce common TIG welding issues like porosity and cracking, ultimately enhancing productivity.
Streamline Workflow
Optimizing your workflow can lead to significant productivity gains in TIG welding. Organizing your workspace to keep tools and materials within easy reach saves time and minimizes disruptions. Creating a clean and organized work environment helps welders stay focused and work more efficiently. Establish clear procedures and best practices to ensure consistency, which, in turn, contributes to a more productive welding process.
Environmental Factors
Environmental conditions like temperature, humidity, and ventilation can affect TIG welding productivity. Excessive humidity, for example, can cause oxidation and contamination, leading to issues during welding. So, welding in a controlled environment helps maintain consistent conditions, reducing the likelihood of defects and rework.
Conclusion
Boosting productivity in welding requires understanding the unique features of MIG vs TIG welding services. MIG welding shines with its speed and efficiency, ideal for large-scale projects, while TIG welding offers unmatched precision and quality, which is perfect for detailed work. Critical factors like proper equipment setup, thorough material preparation, skilled welders, and optimized workflows all boost productivity. By considering these aspects, metal fabricators can enhance their welding operations and achieve better results.
Keep an eye for more news & updates onDiscoverTribune.Org!